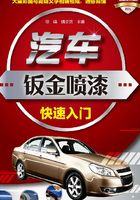
第二节 车身结构与常用材料
在车身修复作业前,需要对事故受损车辆的车身结构和车身材料仔细检查,车身结构和车身材料不同,维修方法也会不同,维修方案也就不一样,因此制订维修方案前需参考维修手册详细了解受损部位的车身结构和车身材料。
一、认识车身结构
车辆发生事故修复时,有时需要拆换零件,拆卸时为了提高效率经常把部件整体(图1-2-1)拆卸,车架式车身拆卸相对简单,整体式车身拆卸相对复杂。

图1-2-1 汽车车身部件分解图
(一)车身结构的类型
车身壳体按照受力情况可分为非承载式、半承载式和承载式(或称全承载式)三种。
1.非承载式车身
货车(除微型货车外),在货车的三类或二类底盘基础上改装成的大客车、专用汽车以及部分越野车,都装有单独的车架。此时车身是通过多个橡胶垫安装在车架上,当汽车在崎岖不平的路面上行驶时,车架产生的变形由橡胶垫的挠性所吸收,载荷主要由车架来承担,顾名思义,这种车身结构应是不承载的。但实际上,由于车架并非绝对刚性,所以车身仍在一定程度上承受着由车架弯曲和扭转变形所引起的载荷。非承载式车身也称为有车架式车身(图1-2-2)。

图1-2-2 典型的非承载式车身
2.半承载式车身
半承载式车身的结构与非承载式车身的结构基本相同,也是属于有车架式的。它们之间的区别在于半承载式车身与车架的连接不是柔性的而是刚性连接,即车架与车身焊接或螺栓固定。
由于是刚性连接,所以车身只是部分地参与承载,车架是主承载体。
3.承载式车身
承载式车身的一个突出特征是没有独立的车架,车身由底板、纵梁、横梁、立柱、车身外覆盖件、围板和车顶板等点焊成刚性框架结构,整个车身构件全部参与承载,所以称之为承载式车身。由于无车架因此也称为无车架式车身(图1-2-3)。

图1-2-3 典型的承载式车身
对承载式车身而言,由于整个车身参与承载,强度条件好,有利于减轻自重并使结构优化。这不仅是当前客车车身发展的主流,而且已经形成了一边倒的设计趋势。
(二)承载式轿车结构
1.现代承载式轿车防碰撞功能
承载式车身没有单独的车架,车身结构件与覆盖件都采用焊接的形式连接在一起,这种设计有助于在发生碰撞事故时保护车内的成员。
承载式车身与非承载式车身的安全性意义是有区别的,非承载式车身用重型低碳钢制成的车架依靠其弧度和刚度抵抗、减弱和限制碰撞损伤,从而起到保护车内成员的作用,碰撞损伤也常局限于碰撞部位周围;而承载式车身依靠全车身的构件和覆盖件整体承受碰撞力,其刚性较大的构件可以将碰撞力传递和分散到车身的各个部位,再由各个部位分别吸收撞击能量。这种结构可能会引起远离碰撞点的车身部件发生损伤变形,因此,在进行承载式车身的检查和修复作业时,要特别注意整个车身总体结构尺寸的变化和各个主要部件的连接状况。如图1-2-4所示,箭头表明了在承载式车身中能量是如何分散开的。

图1-2-4 承载式车身能量传递示意图
一般将汽车分为前、中、后三部分,这三部分刚度是分级的,中部乘客室刚度最高,前部发动机室、后部行李箱室,具有较大的韧性。一般汽车正面碰撞试验(50km/h),前部压缩约30%~40%,而中部仅收缩约1%~2%。
碰撞吸能区是承载式车身中特意做得比较薄弱的区域,以便在碰撞中溃缩。碰撞吸能区对连带损坏有一些控制作用,并使乘客室更加安全,因为它们被设计成按照预定的方式溃缩。
吸能区是用于在高速碰撞中减缓乘客室冲击的前、后段。厚重的箱形立柱和车门梁件用来避免在侧面碰撞中乘客室被侵入变形。
吸能区(图1-2-5)的特征主要表现如下形式:截面突然变窄、截面突然弯曲、梁上有孔洞(非安装孔)、折皱的设计等。维修时,吸能区不能被加强,不能被分割,最好整体更换,如图1-2-5所示圈中是快速更换的螺栓结构。

图1-2-5 吸能区的特征
2. 不同发动机及传动系的驱动方式的轿车车身结构
不同发动机及传动系的驱动方式的轿车车身结构,如图1-2-6~图1-2-8所示。

图1-2-6 前置前驱轿车车身

图1-2-7 前置后驱轿车车身

图1-2-8 中置后驱轿车车身
3.钢板构造与车身安全
(1)前车身结构 承载式车身的前部结构形式和刚度非常关键。车身的前部不仅装有前悬架部件和转向操纵装置,而且装有车辆的动力系统发动机、变速器、驱动轴等。另外,当汽车受到正向冲击时,也靠前车身来有效地吸收冲击能量。因此,车身前部受力相当复杂。要保证车辆的正常行驶,前部车身在构造上不仅要求合理的布置,也要确保足够的强度、刚度,对位置准确度和耐久性、可靠性的要求也十分严格。
前车身主要由翼子板、前侧梁、前围板、散热器支架、发动机舱罩和前保险杠等构件组成,这些部件除发动机舱罩、前翼子板和保险杠采用螺栓连接以外,其他部件多采用焊接以加强车身的强度。
前轮驱动和后轮驱动汽车的前悬架几乎是相同的,两种汽车都使用滑柱式独立前悬架,前车身的精度对前轮定位有直接影响,在完成前车身修理后,一定要检查前轮的定位。
发动机舱罩由内板、加强板和外板组合而成(图1-2-9),外板为空间曲面板,其外表形状与整车造型协调一致。内板由薄钢板经整体拉延后成形,内板筋条网格布置与加强板相似,凸筋的布局既增加美感、提高刚度,又考虑到它们在发动机舱罩上的位置避让诸如铰链、锁机构等零件的需要。

图1-2-9 发动机舱罩
外板和加强板板组合后用环氧树脂胶粘接,内板和外板是折边连接,折边时需在咬合模中进行两次咬合。第一次咬合,将外板翻边45°;第二次咬合,将翻边咬死。也有的内板和加强板用点焊连接。
为了吸振和减少噪声,在内板筋条翻边处与外板内表面还留有2~5mm间隙,将吸振、隔音填料充入其内。
前翼子板(图1-2-10)是轿车前部的大型覆盖件之一,其表面形状与车身侧面造型协调一致,是车身侧面外表的一部分。前翼子板一般由0.6~0.8mm厚高强度钢板拉延成形。其外表形状由车身造型确定,周围边界的形状,前部取决于灯具的形式和布置,后部取决于前部和后部覆盖件的形状,上部取决于发动机舱罩的尺寸和布置,下部与车轮相配合。前翼子板前端大多是用螺钉与车身壳体相连接,后端通过中间板和前围支柱连接,前端和散热器框延长部分及灯具相连接,侧面与挡泥板连接,左、右前翼子板间也有连板。

图1-2-10 前翼子板
(2)侧车身结构(车身中部) 侧车身与前车身和车顶钢板结合而形成乘坐空间。在行使中这些钢板分散来自下车身的负荷到车辆上侧并且防止左右两侧弯曲。此外,侧车身也提供了车门支撑以及万一车辆倾覆时,维持乘坐空间的完整性。因此,为增加刚性,将外板、加强梁和内板组合成一个箱形结构(图1-2-11)。

图1-2-11 车身构件的箱形结构
轿车顶盖是车身轮廓中尺寸较大的大型覆盖件,其作用不只是遮风避雨,提高零件的刚性也是至关重要的,轿车翻车时可起到保护乘员安全的作用,如图1-2-12所示。

图1-2-12 车身顶盖

图1-2-13 轿车车门
车门(图1-2-13)包含了外板、内板、加强梁、侧防撞钢梁和门框。其中内板、加强梁和侧防撞钢梁以点焊结合在一起,而内板和外板通常是以折边连接。另外,车门窗框通常是由点焊和铜焊结合而成,车门形式大致分为:窗框车门、冲压成形车门和无窗框车门三种。
(3)后车身 轿车车身后部是指乘客室后侧用于放置行李、物品的那一部分。三厢式车有与乘客室分开的行李舱[图1-2-14(a)],而两厢式车的行李舱则与乘客室相通合为一体[图1-2-14(b)]。主要有后翼子板、后围板、防撞梁及其后部覆盖件。

图1-2-14 轿车车身后部
行李箱盖由上、下外板及内板组成,见图1-2-15,上外板的形状取决于车身整体造型,它与后翼子板(即后侧围板)形成车身尾部的上表面和左、右侧表面。下外板与后保险杠、后车灯具组成车身后端面外表,同车身的“脸部”一样,与整车造型协调一致,体现造型特色。内板形状复杂,有纵向、横向、交叉和环状筋条,以增加其刚度。

图1-2-15 行李箱盖
(4)下车身结构
①前下车身。如图1-2-16所示,前下车身是由前侧梁、前横梁、转向机齿轮箱支撑梁(有的车型没有)等加强梁所构成,以确保足够的强度和刚性。前侧梁与车底板加强梁及主车底板侧梁相连接,以利于撞击时能将撞击力分散至车身的各个部位。

图1-2-16 前下车身
②中部下车身。中部下车身(如图1-2-17所示)由主车底板侧梁、前车底板下加强梁、车底板横梁、前车底板所组成。主车底板侧梁使用高强度钢板,位于乘客舱两侧下端,又称为车门槛板内板。车底板下加强梁和车底板横梁使用加强件来增强车底板强度和中部下车身的刚性,如图1-2-17箭头所指。

图1-2-17 中部下车身
FF(Front Engine Front Wheel Drive,简称FF,前置前驱)和FR(Front Engine Rear Drive,简称FR,前置后驱)车辆中部下车身的最大差别在于车底板拱起的高度。因为没有后轮驱动组件,所以FF车辆所需要车底板拱起空间没有FR车辆大,因此,能够提供较大的腿部活动空间。如图1-2-18所示。

图1-2-18 FF车辆和FR车辆底部拱起结构的比较
③后下车身。后下车身由后车底板侧梁、后车底板横梁、后车底板所组成。如图1-2-19所示。因为FF车辆燃油箱放置于后座的下方,所以可降低后车底板,而提供既宽敞又深的行李箱空间。当发生后方撞击事故时,大部分的撞击力就可由后行李箱空间吸收。因此后车底板侧梁的后段都经过波纹加工,以提高吸收撞击的效果(如图1-2-20所示)。后车底板侧梁的后段和后车底板侧梁是分开的,以方便车身维修时的更换作业。

图1-2-19 后下车身

图1-2-20 波纹加工设计
当燃油箱固定于车底板下侧(悬浮式),后车底板侧梁后半部具有强韧而不易弯曲的特性,不过在弯角区域(向上弯曲)设计成较容易折损,如此当发生后方碰撞时可保护燃油箱。如图1-2-21所示。

图1-2-21 悬浮式钢板结构
FR车辆的车身以及外部覆盖件与FF车辆类似,此处不再叙述。
二、车身常用制造材料
为了保护环境,车辆的排放要求越来越严格,各种技术的发展促使车辆油耗越来越低,对油耗影响最直接的就是车身重量,降低车身重量是降低油耗最直接的办法。降低重量又不能影响车身安全,材料的属性就要改变。高强度钢、超高强度钢已广泛应用于现在车身。
(一)车身常用钢材
汽车制造使用的钢材主要以钢板材为主,所用板材的厚度根据车身不同部位强度的需要可不同。其中,车身外部结构件常使用0.5~1.2mm厚的板材,车架等车身结构件多使用2~5mm厚的板材。某些重型车辆的车架使用厚度达8mm的钢板。
车身使用的钢板根据制造方法可以分为冷轧钢板和热轧钢板两类,由于制造过程不同,两类钢板在机械性能上存在很大的差异。热轧钢板是将钢锭加温至800℃以上的高温情况下轧延后制成的钢板,厚度较大,车用热轧钢板通常在1.5~8mm之间。热轧钢板的表面质量不是很好,其冷加工性能与冷轧钢板相比要稍差一些,常使用在外观不需要很美观的部分,主要用于车身上较厚结构件的制作,如车架、骨架和梁等构件。
冷轧钢板是热轧钢板再经酸洗处理后在常温下轧延变薄,并进行表面调质处理后的钢板。由于冷轧钢板是在常温下轧制而成,所以它的厚度精度高,表面质量优越,抗拉强度和冷加工性能均较热轧钢板要优良,大都使用在汽车车身、机械零件、电器等表面需要平滑美观的构件上,在悬架周围特别容易受到腐蚀的部位,通常采用经过表面处理的冷轧钢板作为防锈钢板。
车身常用的钢板除少数结构件为中碳钢外,绝大多数的钢板为低碳钢。普通低碳钢含碳量低,材质较软,便于冷加工,可以很安全地进行焊接和热收缩,加热对其强度也不会产生很大的影响。但其抗拉强度比较低,容易变形,而且重量大,不利于降低车辆的总体质量。因此现代汽车上还采用了很多高强度钢材来制造车身上需要承受载荷的部件,既提高了车身的总体强度,又有效地降低了车身的总重量。但高强度钢在进行校正操作时有许多需要注意的地方,如不能过度加热等,因为加热会对其强度造成严重的影响。因此,在进行车身校正时要熟悉所加工的材料的特性,采取合理的方法才能达到良好的维修效果。
另外,为了提高车身总体的抗腐蚀性能,现代车辆上还广泛采用表面处理钢板(主要是镀锌板)等防腐性能优越的材料用于车身上容易发生腐蚀的地方,这些材料在进行维修操作时也有许多需要注意的地方。
1.高强度钢板
高强度钢泛指机械强度高于普通低碳钢的各种类型钢材,并非特指某一种材料。高强度钢的特点是具有高于普通低碳钢板几倍甚至十几倍的抗拉强度,但其质量并没有因此而增加。现代汽车制造追求车身总体质量轻量化、车身总体强度提高以增加安全性,同时还要兼顾防腐性能,因此高强度钢板作为理想材料得到了较为广泛的应用。如图1-2-22所示为整体承载式车身上使用高强度钢的常见位置。

图1-2-22 高强度钢板在承载式车身上的应用
然而,高强度钢板的应用给车身的维修也带来了一定的困难。当高强度钢材料受到撞击产生变形时,由于其强度和硬度非常高,通过简单的校正工艺很难使其恢复原状。在进行普通低碳钢板的校正时,往往采用加热的方法使金属软化以便于整形操作,或进行热收缩操作、释放拉伸应力和焊接等。而使用高强度钢材以后,这种加热则需要严格的控制,有些钢材甚至根本不能使用加热的方法校正,否则会严重影响构件的强度,给车身造成结构上的伤害。因此,在对高强度钢进行校正时需要采用科学合理的方法,通过机械拉伸、有控制地加热甚至局部或整体更换等方法进行修复。
2. 表面处理钢板
表面处理钢板即在普通钢板表面进行处理以提高其耐腐蚀的能力,常用于车身上容易发生腐蚀的部位,如悬架周围、车门的门槛下部、油箱和排气系统等。
3. 金属板的强化
各种尺寸和形状的车身零部件都是由平整的钢板冲压成形的。平整的钢板抵抗变形的能力是较低的,而一旦被冲压成不同的形状,其抵抗变形的能力得到了明显提高。这种通过改变金属板的形状来提高其强度和刚度的方法称为金属板的强化。通常的强化方法有以下几种。
(1)隆起:将金属板冲压成弯曲隆起的形状。这种形状的结构件比平整的结构件可以抵抗更大的弯曲力。
(2)翻边:最常见的如直角折边。对于大面积的车身结构件,通过折边明显可以提高结构件的刚性。
(3)U形槽:金属板被冲压成U形槽后,很难被弯曲,两个U形槽对焊成箱形结构时强度更大。因此车身上重要的结构件都采用这样两种结构,如车架、门槛、车门立柱等。
(二)车用塑料
塑料是以树脂为主要成分,在一定温度和压力下塑造成一定形状,并在常温下能保持既定形状的高分子有机材料。表1-2-1给出了车身常用塑料件ISO识别码、物理性能和修理方法。
表1-2-1 塑料件ISO识别码、物理性能和修理方法
