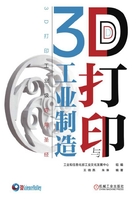
第一节 突破传统制造思维的限制
3D打印/增材制造技术正在加速发展,并成为一种强大的生产技术,但在工业制造中应用该技术的一大障碍是,目前绝大多数的工业设计师所熟悉的制造技术是减材或等材制造技术,他们了解传统制造技术所要求的设计规则,在设计时会根据这些制造技术的特点来调整设计方案,然而对于增材制造技术的特点知之甚少。突破传统制造思维的限制成为增材制造是否能发挥潜力的一大挑战。
多年来形成的规则已经占据了设计师的大脑,这就意味着,当设计师们在设计一件3D打印零件或产品的时候,需要打破以往头脑中所熟知的设计规则,遵循一种满足增材制造技术特点和工艺要求的全新设计思路——为增材制造而设计(DfAM)。
“为增材制造而设计”最常见的定义是:基于增材制造技术的能力,通过形状、尺寸、层级结构和材料组成的系统综合设计最大限度提高产品性能的方法。为增材制造而设计不仅仅是一种设计方法,更是一种策略。在工作中设计工程师会遇到很多挑战,包括如何获得最优的结构形状,如何将最优的结构形状与最优的产品性能相结合,并在设计时将3D打印零件的后处理等工艺对设计的影响考虑进来。
为增材制造而设计离工业制造并不遥远,比如说我国的航天制造企业中国航天科技集团五院总体部针对其3D打印零件进行了点阵结构胞元性能的研究,结合三维点阵在航天器结构中应用的实际情况,提出了三维点阵结构胞元的表达规范,这些研究遵循典型的增材制造设计思路。
可以说,“为增材制造而设计”这一理念的倡导和执行层面的系统建设是当前3D打印向应用端深化的重心和必经之路。
1.理解加工过程
在金属机械加工过程中,加工刀具可以由人工来进行选择,从而制造出特定的细节特征,刀具的大小决定了零件的孔和槽的最小尺寸。在注塑加工过程中,注塑模具的形状决定了产品的形状。
而增材制造过程中发生的各种变化,比机械加工过程要复杂得多。为什么这么说呢?以基于粉末床工艺的选区激光熔融(SLM)3D打印技术为例,金属粉末材料被激光扫描和加热,每个激光点创建了一个微型熔池,金属粉末将经历一个从熔融到冷却凝固的过程。在此过程中,影响零件细节特征的不是刀具,而是激光光斑尺寸和激光器的功率。激光光斑的尺寸以及激光所带来的热量的大小决定了微型熔池的大小,从而影响着零件的微晶结构。
在激光熔融粉末时,必须有充足的激光能量被转移到材料中,将中心区的粉末熔融,从而创建完全致密的结构,但同时热量也会传导超出激光光斑范围,影响到周围的粉末。所以,通常金属3D打印零件的最小的制造尺寸需大于激光斑,超出激光点的烧结量,根据粉末的热导率和激光能量来确定。例如,140μm的点阵结构可使用70μm的激光点来制造,对应壁厚可达到200μm。
当然,金属3D打印技术包括很多,这里我们介绍的仅仅是其中一种:粉末床激光熔融技术,金属3D打印还有很多其他技术,这里不一一分析举例。
而关于塑料3D打印,材料的发展对其应用起到十分关键的作用,工艺方面则因为立体光固化(Stereolightgraphy Apparatus,SLA)、熔融沉积成型(Fused Deposition Modeling,FDM)等技术的快速发展而不断走向更加细致的分支。美国Carbon、惠普(HP)、Stratasys等公司所推出的多样化的3D打印设备,将塑料3D 打印技术推向可以与注塑工艺竞争的水平,无论是从塑料件的性能,还是从尺寸和几何精度的角度来看,塑料3D打印已不再局限于原型制造,而是进入到产品生产制造层面。
2.支撑结构
3D打印技术是一种材料逐层成型,不需要使用模具的制造技术,这为产品的设计带来更大的空间。但是,多数3D打印工艺在制造零件的过程中需要支撑结构,它们将对3D打印产品的设计方式产生影响,并影响整体的制造效率和成本。
比如说在选区激光熔融3D打印技术中,支撑结构起到的作用一是加强和支持零件与构建平台的稳定性;二是带走零件构建过程中多余的热量;三是防止零件翘曲以及降低零件构建过程中的失败概率。在这种工艺中,去除支撑结构的成本在后期处理中可能占总成本的70%,如果要提高增材制造的效率、降低成本,就有必要考虑如何在进行零件设计时最大限度地减少支撑结构的使用。
3.表面质量
不同的3D打印技术带来不同的表面质量,这里面,金属3D打印与塑料3D打印的表面质量处于不同的市场接受度水平。随着加工技术和材料技术的发展,塑料3D打印中的光固化技术以及熔融沉积成型技术,使得用这种技术生产的产品的表面质量越来越接近注塑件的质量。
而金属3D 打印目前还没有达到令人满意的水平。
以常用的选区激光熔融技术为例,在制造过程中,设备的激光束将对金属粉末进行加热,使其熔融,随后经过激光熔融的区域温度下降。在热传导的作用下,微型熔池周围出现软化但没有液化的粉粒。这些粉粒有的被熔融金属吸附,成为牢固地附着在组件表面的颗粒。其他距离热源远的粉末颗粒则未被熔融,仍留在粉末床上。
由于选区激光熔融设备在进行零件增材制造时是逐层铺粉的,在设备进行后一层的激光熔融处理时,将会有一些热量传导到前一层,从而将熔融不完全的颗粒又重新熔融。在这种渐进熔融和冷却的相互作用下,形成增材制造零件表面的特有纹理。
增材制造零件的表面粗糙度与激光功率大小、粉末粒度、层的厚度等因素相关。原则上,通过优化金属粉末和激光参数这样的方式能够改善金属零件的表面质量。但是,通过调节这些因素来提升表面质量与加工时间、加工成本之间存在着一定的关系,在进行调整的时候需要整体权衡。比如说层的厚度越小,表面质量越高,但同时所需要的加工时间会增加,加工成本也随之上升。3D打印金属零件的表面质量也与零件表面的建构方向有关。一般来说,顶面会更光滑。当零件与基板之间的角度变大时,表面会变得更加粗糙。
4.考虑后处理
当前的3D打印零件确实存在着一些先天不足,但部分先天不足可以通过一些后处理工艺来后天补足。以目前在实际生产中应用较多的粉末床金属熔融3D打印技术来说,为了使金属3D打印零件达到所要求的力学性能以及表面质量,在打印完成后往往需要配合使用热等静压、热处理、机械加工、磨削等后处理工艺。
这些后处理工艺将对3D打印零件尺寸产生一定改变,所以在设计一个3D打印产品的初期就应该将需要使用的后处理工艺考虑进去,以便在设计中为后处理工艺留出余量,降低零件的废品率。当然,这些设计思路对增材制造设计师提出了挑战,唯有设计师对将要应用的3D打印工艺充分了解,才能够在设计初期全盘考虑3D打印和后处理对于设计的影响。
比如说,如果一个金属3D打印零件需要通过机械加工提高表面光洁程度,那么设计师在设计零件时就需要考虑材料的去除量,并在设计时补偿,如果在机械加工中需要去除0.05cm的厚度,在设计的时候就需要增加0.05cm,以便后处理后零件符合要求的尺寸公差。当试图进行表面后处理时,设计师还必须考虑过程本身的物理特性,比如说零件棱角位置材料会更容易去除,所以在设计时需要在这些位置加大轮廓度公差。除了外部表面光洁,零件的内腔往往需要一定的畅通性,设计师应考虑这些材料的去除率和补偿。
在进行增材制造设计时,设计师需要考虑两种类型的CAD模型:一种是最终的几何形状,包括基准的确定、加工尺寸公差要求、表面粗糙度要求等;另一个同样重要的CAD模型是供3D打印设备识别加工的模型,这个模型中可补孔,可增加支撑结构,也可以增加加工余量。
通过不同的3D打印工艺加工出来的零件,后处理的思路也不尽相同,这些后处理工艺将反过来影响到设计方案。例如,如果用于制造零件的设备为基于粉末床工艺的电子束熔融(Electron Beam Melting,EBM)3D打印设备,不需要考虑到金属零件与打印基板分离的问题,但需要考虑去除金属粉末和粉末清除处理对设计的影响。如果用于制造零件的设备为选区激光熔融3D打印设备,则需要考虑将零件与打印基板分离切割的问题和消除残余应力的问题。有关后处理工艺对设计所产生的影响以及相关的应对策略的细节将在后面的“后处理”章节中进行介绍。