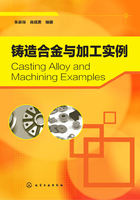
第三节 耐磨钢
耐磨是一个笼统的形容词,工业上通常把耐磨区分为抗磨和减磨,所谓抗磨主要是指润滑介质条件下和有固态介质条件下使金属部件不受磨损,又称作干摩擦及磨料摩擦条件下的抗磨损能力。抗磨部件在冲击力作用下与介质接触而减缓发生部件的磨损(如破碎矿石)称为抗冲击磨料磨损。所谓减磨,工业上如机床导轨与柜架之间的摩擦磨损。不论哪一个摩擦条件,金属表层在外力作用下,不断脱落就构成了磨损,因而磨损的定义应该是外力超过了摩擦副表层分子间的内聚力造成表层分子脱落的结果。摩擦副之间的摩擦力等于摩擦副表层产生的机械咬合与摩擦副表面分子间的吸引力所形成的切向阻力的总合。干摩擦条件下的摩擦力有机械咬合、摩擦副表层分子间吸引力和表层凸峰之间的黏合。当外力超过了摩擦副之间的摩擦力时,摩擦副才能移动。有移动才能有磨损,这就是分子机械摩擦磨损理论。常用如下公式表示:
F=αAr+βN
μ=β+αAr/N
式中,F为摩擦力;Ar为接触面积;N为外加力;α和β为由摩擦副材料表面的物理和机械能所决定的系数;μ为摩擦系数,如以钢和铸铁作摩擦副,其常温μ=0.17~0.23,当升高温度时μ增大,很高温度时材料软化,μ值又降低。对高熔点化合物如WC、MoC、TiC、SiC而言,在600~700℃以上时,μ值反而增大。通常材料的硬度高则抗磨损能力强,高硬度化合物因其固定的价电子关系而表现出较高的抗磨损能力。
一、抗冲击磨料磨损的铸钢材料和工艺
冲击磨料磨损是工程中的一种特殊磨损方式,其过程为:在冲击瞬间,两对磨面在摩擦界面间有硬质磨粒存在的情况下发生相互碰撞,接着两界面进入高应力磨粒磨损阶段;随后,两对磨面脱离接触,不发生磨损。这两个过程周而复始地交替进行。冲击磨料磨损是一种极恶劣的磨损工况,在该工况下工作的零件都表现出极短的寿命。国内冶金、建材、建筑、化工、煤炭和机械行业的机械设备因受强烈的磨料磨损而年耗钢铁易损件数量巨大。目前,常用的抗冲击磨料磨损的铸钢包括高锰抗磨铸钢和中锰低合金抗磨铸钢。
1.高锰钢(Mn13%)
以往冶金学家认为锰加进钢中似乎使钢变脆,英国冶金学家Hadfield将其量超过以往冶金学家认为的合适范围,使钢的含锰量达13%,结果发现此时钢不再显脆性。如果再把这种钢进行适当的淬火,则会变得具有超硬度,可以将它用来制造破碎岩石的机械和用来加工各种金属。普通钢用来制造铁轨,每几个月就要更换一次,但高锰钢铁轨可以连续使用几十年之久。因此迄今这种钢材在全世界仍然被广泛生产应用。在我国称之为高锰钢(ZGMn13),也被广泛地应用在冶金、矿山、水泥、化工化肥、电力、建筑工程等行业。
高锰钢的设计理论根据是:首先Mn在面心立方纯铁中的溶解度是无限的,即Mn元素可以各种比例溶解于γ-Fe中,此外Mn、Ni、Co均可使铁碳合金中的A3温度线下降,A4温度线上升,即极大地扩大铁碳合金的奥氏体区。当Mn增高到一定数值时,可使奥氏体区扩大到室温以下。这三个元素中,以Mn的这种作用为最大。C、N、Cu元素也有一定的类似作用,但不能将γ区扩大到室温,而在较高的温度使γ区封闭起来。所以只靠C、N、Cu是得不到室温奥氏体组织的,它们只能起辅助作用。
高猛钢的特点是具有极好的冲击韧性和兼有表层的加工硬化性能,从而表现出在承受冲击载荷的条件下优越的抗磨损能力。这种表层加工硬化数值通常可达到700维式硬度(HV),恰似中高碳钢淬火后所能得到的马氏体组织的硬度。这种表层显微组织的转变不遵循一般的相变动力学原理,而是表层金属(含Mn、C过饱和的奥氏体)在受到高能激烈冲击时,晶体在切变应力(shearing)作用下转变成高硬度的马氏体。常态下的奥氏体组织硬度在HB150,而马氏体的硬度(与C含量有关)通常可达HRC 60~67。这种硬化层,随着逐层被磨失,又逐层转变成新的马氏体。因此,高锰钢在激烈的冲击性磨损条件下表现出良好的抗磨损能力,从而保证了铸件使用寿命的延长,同时也表现出难于机械加工的特性。
高锰钢(ZGMn13)的另一特点,也可称之为弱点,就是硬化敏感性差。如果所承受的冲击载荷不够大时,或所接触的磨料介质本身的硬度和锐利程度不高时,则其表面的加工硬化性能就不能很好地发挥出来,表面形不成或形成少许高硬度的马氏体层,使抗磨损能力大大减弱。于是表层很快被磨削掉,影响到铸件的使用寿命。各类非自磨式的球磨机(火力发电、水泥磨等)里的衬板,就是处于这种冲击力不大的情况条件下,所以高锰钢衬板在这类磨机里的实际应用中已经充分表现出了它的不适应性。
高锰钢的化学成分:C为1%~1.4%,Mn为12%~14%,Si为0.3%~0.8% P,S<0.04%,国外高锰钢还有添加Cr 0.3%~1.0%,Mo 0.5%~1.0%,Ni 1.0%等。高锰钢在200℃长时间会生成α-(FeMn)3C+ε-(FeMn)3C组织,从800℃以上缓冷必会使(FeMn)3C沿晶界析出ε相,ε相是FeMn金属间化合物,性脆。水冷前钢温必须≥1000℃,从900℃以下激冷,也仍有(FeMn)3C沿界析出。
Mn13%铸钢的生产工艺已众所周知。容易冶炼铸造,要点在于热处理时缓加热(<100℃/h,1050℃水冷固溶极化),净化钢水和低温浇洗法是很有益的。在各国广泛采用Mn13的过程,演化发展出Mn13+Cr1.5~2.5的牌号也得到广泛应用。向原始的Mn13%钢中添加2%左右的Cr元素是出于两种理念,先是借助Cr对C原子的亲和力吸引C原子使钢在凝固后期冷却过程中减缓析出。因为Mn和Cr同属于过渡族元素,它的原子的电子层未填满的程度都比铁原子的电子层未填满的程度大,所以Mn和Cr原子都比Fe对C原子的亲和能力强,而易生成碳化物[MnC,Cr7C3,(FeCr)3C,(FeMn)3C等]。又因Cr和C的亲和力大于Mn和C的亲和力,当铬<2%时与碳化合成(FeCr)3C,当铬>2%,易生成(CrFe)7C,碳铬都很高时生成Cr13C6。在钢水凝固和冷却过程中,钢中的铬对碳原子有吸引力,阻止和减缓碳原子析出。随着C在奥氏体中溶解度的下降,总是会有一部分铬和锰与碳生成初碳化物沿奥氏体晶界析出,但是已知铬在1000℃奥氏体中的溶解度是12.8%,即使钢的温度下降到室温,钢中奥氏体终归会有一些铬原子吸引一些碳原子留在奥氏体内,从而减少奥氏体晶界上碳化物的数量,从这个概念上看,向Mn13%钢中加入2%的铬是有益的。其次借助13%的锰获得的奥氏体组织,其耐蚀性较利用铬镍元素获得的奥氏体组织的耐蚀性低很多,故高锰钢在大气中和在其他带有酸碱性的介质中容易表层锈蚀,而加快磨损。含铬2%左右的高锰钢经水韧处理后Cr原子溶在奥氏体中,无疑可增强或改善Mn 13钢的耐蚀性,以利延长铸件使用寿命,作者认为这应是把原始的Mn 13%钢发展生成Mn13%+Cr2%牌号的理论根据或者说是出发点。实际应用证明含Cr 2%的高锰钢铸件有较好的效果。所以,欧美企业向中国购买矿山作业的高锰钢铸件无一不是要求含铬1.5%~2.5%的。
2.中锰低合金钢
笔者曾系统地研究了生产实践中不同类型的中锰(Mn 3.5%~10%)低合金抗磨铸钢材料和相应工艺,主要是奥氏体+马氏体铸钢和全奥氏体基体时效硬化的铸钢。通过与传统的高锰钢铸件在同一工作条件的对比,所得结果如表2-7所示。矿山使用证明中锰低合金铸钢件的抗磨性比传统的高锰钢铸件提高50%~200%。
表2-7 不同锰含量的铸钢相对耐磨性的对比

生产实践证明,中锰低合金铸钢用于高层建筑工地上混凝土输送管道的弯头,其使用寿命由传统高锰钢弯头工件的2000t提高到4000t以上,最高曾达1×104t的寿命,而铸件生产成本却低于类似的传统高锰钢。
通过对比不同锰含量的铸钢可以发现,固溶时效强化的高碳低合金的中锰奥氏体铸钢具有更大的实用价值。在使用之前,须经过人工时效处理使铸件整个截面得到一定的硬化,以提高铸件的初始硬度。在使用过程中,又因其具有较敏感的加工硬化性质而使铸件表层发生再一次硬化,则显然有利于延长铸件使用寿命。
研究和发展中锰低合金铸钢的科学依据有如下几点:首先锰、镍、钴都能扩大和稳定γ铁区到室温以下。Hadfield钢(Mn 12%~14%,C 0.9%~1.2%,也就是我国通常称的高锰钢)的马氏体转变温度是-150℃,这说明即便在室外作业,所需的奥氏体组织的抗磨钢只要它的Ms点不高于-50℃就能保持其高冲击韧性,也意味着降低锰含量会降低奥氏体的不稳定性而容易发生加工硬化,使之适于更广泛的工作条件。此外当中锰奥氏体中含有过饱和的碳、钒、硼、铜等任一能发生沉淀硬化作用的因素都会引起钢的晶格畸变(如原子脱节、空位、各种位错等)从而增大晶面滑移阻力,有利于增高钢的抗磨性能。
中锰低合金抗磨铸钢(100Mn7CrNiCuTiRE)的化学成分分别为:C 0.9%~1.2%,Si 0.4%~0.6%,Mn 6.5%~8.0%,Cu 0.6%~0.8%,Cr 0.8%~1.3%,N 0.02%~0.05%,Ti 0.2%~0.35%,RE 0.05%~0.1%,N、Cr 0.04%~0.05%,S、P均≤0.04%。
冶炼工艺为:采用中频炉或电弧炉设备,冶炼工艺同ZGMn13;所需炉料为高碳或中碳铬铁(Cr>60%),锰铁(Mn>65%,C>7%),氮化铬铁(N 3%~10%,Cr>60%,钛铁Ti 28%~30%),稀土合金(RE 24%~31%);出炉前5~10min用铝脱氧,随之加入预热过的氮化铬铁(粒度<20mm),迅速升温到1620℃以上。出炉温度≥1600℃,浇铸温度1480~1520℃,稀土合金和部分钛铁(各0.2%~0.3%占铁水量)做变质处理用,粒度<10mm(其余入炉的钛铁粒度可大些)。变质处理方法:将所需的稀土合金0.2%~0.25%及钛铁0.2%~0.3%(均占钢水总量),称量准确后,均匀化,分成两等份,一份置于包底,一份随钢水冲入包内。钢包注满后,须采用集渣剂除渣与挡渣。
热处理一般采固溶加时效处理,固溶处理工艺类似ZGMn13,升温速度<350℃阶段,升速应<80℃/h,350℃以上时,≤100℃/h,在720~750℃保温1.5h,然后再升到1050℃保温3~4h,铸件淬火温度1030~980℃,淬火后将铸件在380~420℃,保温6~8h,出炉空冷。
经以上冶炼及热处理后的样品,其力学性能如下:冲击韧性αk>80J/cm2,水韧处理后铸件硬度可达HB150~160,时效后硬度HB>200,铸件使用后表面硬度HV600。经检验其显微组织为细晶粒(4级以上)奥氏体基体+弥散的碳化物微粒子。
中锰低合金抗磨铸钢除了100Mn7CrNiCuTiRE外,还有120Mn7Cr2NTiV和120Mn7Cr2NTiNb,生产工艺与前者基本相同,其化学成分如下。120Mn7Cr2NTiV:碳1.0%~1.4%,锰6.5%~8.0%,铬1.5%~2.0%,氮0.02%~0.05%,钛0.20%~0.35%,钒0.25%~0.4%,硫磷均≤0.04%;120Mn7Cr2NTiNb:碳1.0%~1.4%,锰6.5%~8.0%,铬1.5%~2.0%,氮0.02%~0.05%,钛0.20%~0.35%,铌0.1%~0.15%,硫磷均≤0.04%。此类含钒0.2%~0.4%或含铌0.1%~0.15%的中锰钢,经水淬固溶后的奥氏体晶粒度可细化至5级或6级,一改传统高锰钢历来的粗大晶粒特性(多是1级甚至于无极的粗大晶粒度,铸件容易发生冷裂),据笔者的实践中发现中锰抗磨铸钢的主体元素(碳铬锰)的最佳值宜取C 1.2%,Cr 2.0%,Mn 7%~7.4%。
二、抗热疲劳剥落与磨损的铸钢
在高温下服役的机件,由于局部温度的变化引起机件自由膨胀或收缩受到约束时,就会引起热应力,而由周期变化的热应力或热应变引起的材料疲劳破坏现象,称为热疲劳,也称热应力疲劳。金属轧制加工时所采用的热坯轧辊则应用在这种典型环境下。热坯初轧机和各种型钢、板钢粗轧机架的轧辊生产广泛采用铸钢材料制成,并不断地有新型钢种被开拓和使用以延长轧辊的寿命和增加生产效率。
当轧辊与1200~1250℃炽热的钢坯(或锭)接触时,轧辊表面受到钢坯传递的热量和轧辊与钢坯之间摩擦产生的热使轧辊表层1mm左右深度的温度骤然升高。据计算和测试,接触区轧辊表面可升高到700℃左右。随着轧制的过程,轧辊表面这一高温又迅速与热钢坯脱离接触,进入喷水冷却区,轧辊表面温度又急剧下降,轧辊每转一周,其表面上的接触点都经受一次激热和激冷的变化,这是与轧辊转速同步的周期性的激热和激冷。当轧辊表层升温到700℃时,引起表层膨胀。此时轧辊内部尚处于低温状态因而使表层膨胀受阻,导致表层经受压应力。有关研究文献指出这种压应力可达500MPa,当轧辊层受到激冷时此表层又变成经受拉应力。如上反复循环使轧辊表面接触点上在经受多次突变应力作用之后发生热疲劳网状裂纹。热裂纹发生严重时可导致轧辊断裂,这是影响轧辊寿命的主要问题。此外,轧辊表面与热环境接触点在重大压力下进行带有一定滑动摩擦性质的滚动摩擦,又不可避免发生峰谷机械咬合、热点黏合和分子面吸引黏合等摩擦力,而使轧辊表面受到磨损。
为了延长辊身表层发生热疲劳裂纹和减少磨损,要求轧辊的材质应有较高的常温屈服强度和断裂强度,较高的高温(700℃)抗压缩屈服强度和抗磨损能力。具有这种特性的材质,其显微结构应该是在强韧而又稳定(不因辊身表面接触点温度变化而发生相变)的基体上嵌有均匀散布的高硬度质点所组成。生产出具有这种理想的显微组织的轧辊不仅须有适宜的化学成分组合,还需要有适宜的冶炼、铸造、热处理工艺为保证。除了要求轧辊材质优越之外,经济的生产成本也是必须的条件。
为了满足热坯轧辊生产工艺上各种条件的要求,笔者研制开发了特种铸钢(代号HG151)。其化学成分为%:碳1.4%~1.6%,硅0.3%~0.7%,锰0.6%~0.9%,铬1.0%~1.4%,镍0.5%~0.9%,铜0.3%~0.6%,硫<0.035%,磷<0.035%。其具体熔炼工艺为:待废钢等金属炉料全溶后,升温到1550~1580℃取样化验C、Si、Mn、S、P;扒开氧化渣,加入铜块(块度小于40mm)、镍板和铬铁(块度小于80mm),全熔后保温10min以上,使合金元素扩散均匀,然后取样化验C、Cr、Ni、Mo、Si、Mn、S、P,加适合炉衬材料的覆盖剂并在1550~1580℃保温;调整化学成分后向炉内加入0.1%的硅铁进行预脱氧,然后加入铝块0.05%,搅拌后扒渣,测温。1550℃出钢,钢包预热到400~700℃以上,出钢时加入预热到200℃以上的稀硅铁合金0.2%(粒度5~10mm)撒在钢水流上冲入钢包中。钢水面上洒入覆盖剂,静置5~8min测温,当钢水温度在1520~1530℃时,扒净渣浇铸。在铸造轧辊时为防止局部发生缩孔或疏松等缺陷,应采用如下凝固的条件。
(1)采用上注法进行浇铸。
(2)下辊颈采用整体外冷铁型,内壁挂砂15~25mm,原则上采用树脂自硬砂[可用硅砂,含SiO2>96%,粒度50~100目,加树脂(1.5%)、固化剂(33%×1.5%)],也可用铬矿砂(含Cr2O334%~48%,SiO27%~10%)代硅砂。
(3)辊身采用铁型,内壁喷涂料1mm。涂料成分为锆英粉100+膨润土2%+糊浆3%+水,烘干。
(4)上辊颈和冒口采用砂型铸造,砂型厚度≥50mm。冒口部位采用绝热材料以保温,浇铸后期点浇冒口并捣压冒口。
(5)轧辊的铸坯直径(辊身和上下辊颈)均需要按成品轧辊图纸上规定的直径加大15mm,作为热处理后氧化脱皮和脱碳层(以10mm计)及机加工余量(5mm计)。
(6)辊身和下辊颈所用的铁型壁厚相同,均等于辊身铸坯直径的一半,上辊颈和冒口的砂箱可按一般壁厚。
(7)轧辊铸坯的下辊颈长度按图纸规定的长度加长15mm。
(8)浇铸轧辊后,使铸坯在型内缓慢冷却36h以后开箱,即时送入预热到200℃以上的热处理炉中进行热处理。
(9)对处理后的轧辊辊身轴向表面硬度和材质性能的检测。对已热处理的轧辊毛坯进行加工,加工后的辊身直径应大于规定尺寸1mm,不得小于规定的直径。轧辊经机加工后,除检查有无气孔、砂眼、夹渣铸造缺陷之外,还须在车光的辊身表面沿轴向测定肖氏硬度,每隔100mm测一点。辊身表面的硬度应≥HS37,辊颈的硬度可略低辊身,拉伸强度σ≥780MPa,布氏硬度HB≥280。
已有的生产实践证明,具有以上力学性能的铸钢材质和制成的热坯轧辊的使用寿命可比70Mn2轧辊的使用寿命延长一倍左右,全寿命的轧钢出材数量相当于70Mn2和无限冷硬铸铁轧辊的两倍左右。
锰铬钼钛热坯轧辊用钢的化学成分:碳0.7%~0.78%,硅0.3%~0.6%,锰7.8%~8.8%,钼0.3%~0.8%,铬0.8%~1.2%,钛0.2%~0.3%,稀土0.02%~0.04%,硫≤0.035%,磷≤0.035%。其具体熔炼工艺如下所述。原料:废钢(中低高碳、合金钢均可,硅钢片除外),高碳锰铁(Mn50%),钛铁(Ti30%),稀土硅铁合金(RE30%);废钢熔后加入锰铁4kg/100kg钢水,全熔后扒渣,加入铬铁2kg/100kg钢水,升温到1550℃,钛铁、铬铁熔化后加钛镁1kg/100kg,扒渣,取样分析C、Si、Cr、S、P;调整成分加覆盖剂(珍珠岩或石灰石分+萤石粉2:1),保温1550~1580℃,30min使成分均匀。1550~1580℃出钢。其浇铸工艺:用钢水上浇铸,浇铸温度1500~1520℃(原则上低温浇铸);加覆盖剂后钢水在包内静置10min,测温后浇铸;钢水包最好用底注式,包底一侧(对出钢槽方向)放入铝0.05%脱氧和稀土合金0.3%,粒度5~10mm。浇铸后,点冒口补缩;轧辊在型内冷却30h之后开箱,立即送入热处理炉内,进行热处理。辊身经机加工后,测成分、拉伸强度、屈服强度、延伸率,布氏硬度HB≥240,显微组织为层状细珠光体基体和少许粒状化合物;机加工后,辊身直径应大于图纸尺寸1mm,不可小于图纸尺寸。
三、抗流体耐蚀的铸钢
这里所说的抗流体耐蚀是指广泛应用于有色和黑色金属矿山的杂质泵,火力发电厂用的污水泵,煤矿用的煤水泵以及化工、化肥业用的耐酸、耐碱泵的泵体与叶轮材料,它们要经受液体腐蚀和固体磨损的共同作用。这里只介绍高铬抗磨蚀铸钢和低合金抗磨蚀铸钢的冶铸工艺。
1.高铬合金抗磨蚀铸钢
该钢材主要参考了欧美各国广泛采用的高铬钼铜(Cr15%,Mo3.0%,Cu2.0%)材料,结合我国资源情况,研究出此抗磨蚀新材料和铸件工艺。其生产工序为:熔炼→铸造→清理→软化退火→机加工→硬化处理→安装使用。
该钢材化学成分:C 1.6%~1.8%,Si 0.4%~0.8%,Mn 0.4%~0.8%,Cr 23%~26%,Mo 0.4%~0.5%,Cu 0.5%~0.8%,RE 0.02%,S<0.04%,P<0.04%;熔炼与铸造工艺:出钢前应脱氧和镇静,有条件时化验与调整成分;该钢含碳量较高,浇铸温度适当降低到1530~1550℃;炉前做变质处理:RE 0.2%,Si-Ca-Ba 0.25%,粒度<5mm,采用冲入法;浇包使用时预先加热到>400℃;砂芯应具有良好退让性;具体铸造工艺设计因件而定;去除冒口,防止用锤击打。
热处理工艺为机加工前采用软化退火,以<100℃/h升温速率升至650℃保温1.5h,然后升温至950℃保温1.5h,后以<100℃/h降至700℃后随炉冷却。在机加后须进行硬化处理:以<100℃/h升温速率升至650℃保温1.5h,然后升温至1050℃保温1.5h,降至540℃保温1h,后以<70℃/h降至100℃,后以<80℃/h升至440℃保温6h随炉冷却。铸态钢材硬度为HB450,退火后HB350~400,硬化后HB≥600。
2.低合金抗磨蚀铸钢
该钢材可用于输送金砂粉矿浆用三通弯管,其化学成分为:C 0.6%~0.7%,Mn 0.8%~1.2%,Cr 0.8%~1.2%,Mo 0.3%~0.4%,Cu 0.3%~0.4%,Si 0.4%~0.8%,RE 0.02%,S≤0.04%,P≤0.04%。熔炼工艺:炉料为优质废钢,高碳锰铁,高碳铬铁,镍板,钼铁,纯铜,稀土,硅铁,硅钙钡合金;废钢熔后加锰铁、铬铁、熔通后扒渣,加入其他合金材料,升温到≥1600℃取样分析C、Si、Mn、Cr等元素;调整成分,加覆盖剂保温30min并脱氧;出钢温度1560~1580℃,冲入变质剂RE 0.2%,Si-Ca-Ba 0.25%,粒度<5mm,浇包预先加热>400℃,浇铸。造型工艺由厂家设计。热处理时,依次在650℃、1050℃、780℃、860℃、650℃保温1.5h、2h、4h、2h、4h后空冷降温,热处理炉内四角处,堆放一些焦炭,保持还原性或弱氧化气氛。热处理后机械加工,铸件的力学性能:HB350,σb为800~900MPa,δ为8%~10%,具有良好的综合性能,弯管的使用寿命≥3年。