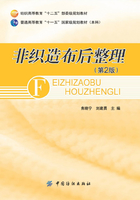
第三节 烧毛
烧毛工艺是利用火焰的作用,去除凸起在布表面的浮起纤维,使非织造布获得光洁表面的一种整理方法。烧毛整理在非织造布中有很多应用。过滤材料经烧毛处理可以避免纤维脱落,提高过滤性能,还可使“滤饼”易于剥离,延长使用时间。医用卫生材料经过烧毛处理可减少纳污吸尘能力,防止细菌感染;采用印花制得的非织造布年历、地图、壁挂等经烧毛处理,可使花纹清晰,轮廓突出。除此之外,土工布、床单、桌布、沙发靠巾等也可进行烧毛整理。
一、烧毛机理
烧毛就是使非织造布快速通过火焰或擦过炽热的金属板表面,以去除表面的绒毛而获得光洁表面的工艺过程。非织造布表面的绒毛由伸露在布面的纤维末端或完全裸露在布表面的纤维组成。当布在火焰上迅速通过时,布面上分散存在的绒毛由于体积小、蓄热能力差,能很快升温,并发生燃烧;而布本身厚实紧密的产品,蓄热能力大,升温较慢,当布温未达到着火点时,已经离开了火焰,从而达到既烧去绒毛,又不损伤布本身的目的。通常认为绒毛与布本身的温度差越大,越有利于烧毛。因此,目前倾向于在使火焰具有足够强度的条件下,合理加快车速。在烧毛过程中,要把握以下几点关键问题。
(1)依据纤维本身的热熔性以及非织造布本身的膨松性,合理调节温度。一般,烧毛火焰温度,棉为800~850℃,涤纶为480~490℃(或560℃),羊毛为600℃(或720℃)。
(2)控制非织造布运行速度,尽量减小非织造布与火焰的接触时间,以高热能火焰迅速导向非织造布进行烧毛。
(3)烧毛后应迅速移除布本身所吸收的热量(一般采用吸冷风的方式),以防止不必要的热损伤。
(4)火焰的热量应均匀一致,防止烧斑产生。
二、烧毛机
烧毛设备分为气体烧毛机和热板式烧毛机两种。非织造布烧毛设备与普通纺织品的基本一致,常采用气体烧毛机,而热板式烧毛机由于与布直接接触摩擦,易使布面擦伤,且烧毛不匀,故不常用。
气体烧毛机具有结构简单、操作方便、劳动强度低、热能利用充分、烧毛质量好、适用性广的特点,所使用的可燃性气体主要有城市煤气、液化气、汽化汽油气、发生炉煤气、丙烷、丁烷等。
气体烧毛机通常由进布、刷毛、烧毛、灭火、冷却和落布等装置组成,如图5-8所示。
图5-8 气体烧毛机示意图
1—刷毛装置 2—烧毛装置 3—灭火装置 4—冷却装置 5—刷毛辊 6—烧毛火口 7—冷却风 8—灭火毛刷 9—刷毛辊
1.刷毛装置 刷毛装置主要刷立非织造布表面绒毛,使其利于灼除,同时刷除附着于非织造布表面的纤维屑及尘埃杂质。
刷毛箱内装有4~8个猪鬃毛或尼龙刷毛辊,非织造布在两排垂直排列的刷毛辊之间自下而上运动,毛刷则与非织造布逆向高速回转。为防止上辊刷下的绒毛尘埃杂质掉至下辊,上、下相邻的两辊间应隔有挡尘板,使绒毛等落入尘箱,并被除尘装置吸走。
2.烧毛装置 气体烧毛机一般为单层单幅烧毛,火口数量为2~6只,视产品品种、烧毛要求和火口烧毛效率而定。烧毛部分一般包括燃气输送管道、空气与燃气混合室及烧毛火口。可燃性气体必须与空气以适当比例混合后才能完全燃烧。在生产中,可通过观察火焰状态和颜色来判断燃烧是否正常。以城市煤气来说,火焰应为光亮有力的淡蓝色。
烧毛火口是气体烧毛机的关键部件,直接影响着烧毛效果和效率。优良的火口应满足下列要求:火焰温度高,能达到1300℃以上;火焰整齐有力,穿透力强;火口自身热损小,能耗低,维修容易,寿命长,操作方便。一般采用狭缝式火口,这种火口可利用几何尺寸的突然缩小产生高速输出的燃气,保证火焰力度。另外,还提供了小面积的燃烧,保证非织造布受热时间短,起到保护布的目的。狭缝式火口是一铸铁小箱体,如图5-9所示,可燃气体(含空气)由进气管2进入火口的混合室3中,利用涡流再一次混合后,由火口缝隙1喷出燃烧形成的高温窄条火焰。狭缝的宽度按可燃气体燃烧速度的快慢加以调节。为防止金属火口体上部温度过高而变形,一般都须采用流动冷却水来降温。
图5-9 狭缝式烧毛火口
火口间隙可根据燃料不同,事先进行调节。一般煤气烧毛火口的间隙为0.7~1mm,丙丁烷烧毛火口的间隙为1.2mm,汽油气烧毛火口的间隙为0.6~0.8mm。
合成纤维非织造布在烧毛时,必须充分考虑纤维的热性能及其较为蓬松的结构特点。如PET纤维在230~240℃时软化,255~260℃时熔融,而在480~490℃时燃烧,并且它虽能被火焰点燃,但一经离开火焰,就很快中止燃烧。所以必须有足够的热能迅速传给它,并迅速达到燃烧温度,才能使PET纤维材料表面的绒毛完全燃烧。否则,如果火口供给的热能不足或供给热能速度太慢,PET纤维将首先熔融,致使纤维收缩而不能完全燃烧,从而在非织造布表面产生熔球现象。
3.灭火装置 非织造布经烧毛后沾有火星,如果不及时熄灭,往往引起焚烧。灭火装置的作用是灭除从烧毛装置出来的非织造布表面的残留火星。一般可选用毛刷、轧辊或蒸汽灭火方法。蒸汽灭火是利用向非织造布表面喷射水蒸气,达到灭火的目的。毛刷灭火是利用尼龙刷辊刷除残余火星,适宜刷除化纤布烧毛后的残余焦粒。
4.冷却装置 为了防止烧毛后非织造布在干态折叠过程中产生折痕,需对非织造布进行降温。冷却装置可以是通有冷水的冷却辊,也可采用喷风冷却装置。
三、烧毛工艺及质量评定
决定烧毛效果的因素有车速、火焰温度、非织造布与火口的距离、非织造布与火口的接触形式及火口数量等。
1.车速 车速的快慢与温度联系紧密。调节车速实际上就是控制非织造布与火焰接触的时间。车速越低,加热时间越长,非织造布幅宽收缩越大,纤维越容易受到损伤。合成纤维尤为明显。车速加快可提高生产效率,但也容易使非织造布受到较大张力,甚至被拉断。一般车速为40~80m/min。非织造布定量越小或布中合成纤维含量越高,则车速越快。在烧毛过程中还应注意车速要均匀,否则易造成与气压不匀类似的由烧毛不匀而产生的疵点。
此外,车速还应根据火焰强度及火焰与布的间距而定。如火焰强度高,火焰与布的间距小,车速应快些,反之可慢些。通常认为绒毛与布本身的温度差越大,越有利于烧毛。因此,目前倾向于在使火焰具有足够强度的条件下,合理加快车速。
2.火焰温度 火焰温度越高,烧毛效果越好。烧毛温度的高低要以绒毛烧掉而布面不受损为宜。这里所指的温度包括火焰温度和火口辐射热的总和,或者以布面温度为准。温度过高会损伤纤维。火焰温度的高低可用热电偶或其他无接触温度计测定。但一般也可以用目视的方法(色温)推断,火焰竖直有力,呈短波长色光(青蓝色),为800~900℃;火焰软,呈长波长色光(橘红、金黄),为650~750℃。火焰温度的高低由空气及可燃气的配比决定。
烧毛温度与纤维成分、非织造布结构、定量等有关,耐热性好的纤维可高些,反之,可低些,结构厚密时可高些,结构轻薄时可低些。
3.非织造布与火口间距离 距离越近,绒毛烧掉得越彻底,但非织造布不能距火口太近,更不能直接擦过火口,否则会引起非织造布损伤,强力下降。一般可将距离设定在5~80mm之间。
4.火焰与非织造布的接触形式 烧毛整理一般分为轻烧、中度烧、重烧三种,可通过调节火焰与非织造布的接触形式来实现,如图5-10所示。
图5-10 火口与非织造布的接触形式
轻烧可采用切烧方式,适合于不耐温且轻薄的非织造布;中度烧可采用对烧的方式,适合于中等定量的化纤或混合纤维非织造布;重烧采用透烧的方式,适合于厚重且结构紧密的天然产品。新式烧毛机应该具有火口角度调整装置。
烧毛加工不当会造成烧毛过度,使非织造布强度降低。所以,需要有一些质量评定方法,对烧毛效果进行评定。烧毛质量的评定方法是在非织造布强度符合要求的前提下,将其平放在光线较充足的地方,观察布面上的绒毛情况,按五级制进行评定。1级为原布未烧毛;2级为布面上长毛较少;3级为布面上基本无长毛;4级为布面上仅有较整齐的短毛;5级为长短毛全部烧净。针刺过滤材料的烧毛达到3~4级即可。
四、烧毛产品应用
针刺非织造布过滤材料系三维结构材料,孔隙小且分布均匀,总空隙率达70%~80%,其特点是除尘率高、透气性能好、清灰容量大、使用寿命长、对粉尘具有较强的截留和阻挡作用,比用机织物制成的二维结构滤料具有更加优越的过滤性能。它能快速形成“滤饼”,增大过滤作用,遏制粉尘粒子向深层的渗透,同时提高了滤材的过滤效率和使用寿命。如果对滤材表面进行烧毛处理,使烟尘积集于滤材表面,便于清除“滤饼”,又不会堵塞非织造布内部孔隙,从而延长了滤材的使用寿命。下面是针刺滤材进行烧毛整理的应用实例。
(一)涤纶易清灰针刺毡和耐高温美塔斯针刺毡
涤纶易清灰针刺毡是一种常温针刺滤材,其主要原料为聚酯纤维;美塔斯针刺毡是目前常用的耐高温针刺滤材。它主要原料是美塔斯纤维,其中还混合少量的涤纶(5%)和PPS纤维(5%)。美塔斯纤维是一种化学结构稳定,且具有优异的耐温性、耐燃性及高温尺寸稳定性的纤维。其玻璃化温度为220℃,而碳化温度为400~430℃。在烧毛过程中,滤材表面绒毛炭化变黄变焦,因此美塔斯针刺滤材烧毛前后色泽变化较大。
上述两种滤料整理前定量为500g/m2,采用先烧毛再轧光的整理方式。烧毛采用气体烧毛机,双喷射火口,热源为城市煤气,压力为0.66×105Pa,烧毛工艺见表5-2,轧光工艺见表5-3。
表5-2 两种针刺滤材的烧毛工艺
表5-3 两种针刺滤材的轧光工艺
整理前后,针刺滤料的过滤性能分别采用尘埃粒子计数法和钠焰法测量,数据见表5-4。尘埃粒子计数法中尘埃的粒径分别为0.3μm、0.5μm、1μm、3μm、5μm和10μm六个级别,流量为2.83L/min;钠焰法粒径为0.07~0.26μm,流量为84L/min。
由表5-4数据可知,滤材经过烧毛、轧光整理后,过滤效率有所提高。以钠焰法测试的滤料效果尤其突出,提高达100%之多。这是因为在空气过滤过程中,尘粒除了在进入纤维层时被捕获外,在过滤材料的表面还能形成一层尘埃滤饼,它起着一种高效的过滤作用。经过烧毛、轧光整理后的针刺滤料表面平滑,迎尘面成致密状态,易形成滤饼,使其容量增大,捕尘效率高,过滤速度加快。因此,提高了针刺滤材的过滤效率。另外,从经济效益的角度来看,经过整理的滤材表面光滑,可使形成的滤饼容易剥离,并达到容易清灰的目的,清灰后的滤材可再次使用,从而提高了针刺滤材的使用寿命。
表5-4 两种针刺滤材整理前后的过滤性能
整理前后针刺滤料的透气性能和拉伸性能见表5-5。
表5-5 两种针刺滤材整理前后的透气性能和拉伸性能
由表5-5可知,两种滤材经过烧毛、轧光整理后,透气性能有所降低。一般未经整理的滤材,由于针刺后相互抱合的纤维自身弹性回复的作用,使纤维间保持一定的距离,相互间的缠结不太紧密而留有孔隙,因此,滤材相对蓬松,其透气性能远远好于经过整理的滤材。
在烧毛过程中,尽管烧毛时间短,由于火焰温度很高,不可避免地会使滤材表面部分纤维发生不均匀熔融,有可能形成熔结斑块。再经轧光,虽可以使厚度均匀,但熔融结块不可能消除,且滤材内部结构也变得紧密,纤维间空隙减小,因此,经过整理后,滤材的透气性能会有所下降。
另外,从反映试样性能均匀性的离散系数上也可发现,未经整理的滤材离散系数小,而经过整理的滤材离散系数大。这是因为,未经过整理的滤材,其均匀性主要受梳理机构的影响。当梳理成网及针刺工艺较为合理时,可保证滤材具有较高的均匀性,因而透气量的离散系数就比较小。而经过整理的滤材,由于其在整理过程中受诸多因素的影响,其产品的均匀性不易控制。如烧毛过程中,火焰的大小、进布速度及轧光中的温度、压力等,这些因素的作用使产品透气性能呈现出不均匀性。
总之,针刺滤材进行烧毛轧光整理是提高其过滤性能和使用性能的重要手段,经过整理的滤材表面平整光滑,过滤效率高,易于清灰,减少更换次数,提高滤材的使用寿命。特别是滤材的内部堵塞得到缓解,在使用气流反吹清灰时,反吹气流的压力不必过大,大大降低了能量消耗。
(二)涤纶针刺滤料和丙纶针刺滤料
对涤纶针刺滤料分别进行轧光,烧毛及烧毛—轧光的整理方式。对丙纶针刺滤料进行轧光,烧毛—轧光的整理方式。
整理后的滤料的过滤性能使用LC滤材静态过滤性能测试装置进行测定,过滤速度为1.5m/min,采用325目(粒径范围为2~43μm,主体粒径约7.5μm)滑石粉作为标准粉尘,该粉尘密度为2.82g/cm3,发尘量为20g/8min,测试结果见表5-6。
表5-6 经过不同后整理滤材的透气性能和静态过滤效率
从表5-6中的数据可以看到,未经整理的滤材过滤效率为99.6%,经整理后过滤效率均有提高,而且都保持在很高的水平上,尤以烧毛后轧光最为突出达99.99%。所以烧毛、轧光整理提高了滤材的过滤效率,但必须牺牲滤材的一部分透气性能,考虑这一影响对滤材使用厂家提高设备负载能力并降低能耗是很有意义的。通过测试,经过整理和未经整理的滤材透气量q有如下关系:q未整理>q烧>q烧—轧>q轧。