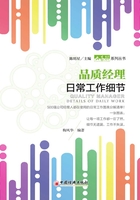
3.6 全面质量控制制度描述
全面质量控制制度
总则
第一条 目的。
为保证质量管理工作的顺利开展,及时发现并且迅速处理问题,以确保提高产品质量,使之符合市场的需要,特制定本制度。
第二条 质量控制目标。
1. 实现全年无重大质量事故。
2. 实现一等品率达99%以上。
3. 创建优质品牌形象,提供一流的质量服务。
质量控制标准及检验标准
第三条 质量控制标准及检验标准的范围。
1. 原料质量标准及检验标准。
2. 半成品质量标准及检验标准。
3. 产品质量标准及检验标准。
第四条 质量控制标准及检验标准的制定。
1. 质量控制标准。品质部会同生产部、营销部、研发部及有关人员依据“操作规范”,并参考国家标准、行业标准、国际标准、客户需求、本身制造能力以及原料供应商水准,分原料、半成品、产品填制质量控制标准及检验标准制(修)定表,一式两份,报总经理批准后,由品质部留存一份,研发部留存一份,并交有关单位凭此执行。
2. 质量检验标准。品质部会同生产部、营销部、研发部及有关人员,分原料、半成品、产品将检查项目规格、质量标准、检验频率、检验方法及使用仪器设备等填注于质量标准及检验标准制(修)定表内,交有关部门主管核签并经总经理核准后,分发给有关部门。
第五条 质量标准及检验标准的修订。
1. 各项质量标准、检验规范的修订。因设备、技术、制造过程、市场需求以及加工条件变更等因素变化时,可予以修订。
2. 品质部每年年底前至少重新校正一次,并参照以往质量实绩,会同有关部门检查各规格的标准及规范的合理性,并予以修订。
3. 质量标准及检验标准的修订流程。品质部应填写质量标准及检验标准制(修)定表,说明修订原因,并交有关部门主管核签。报总经理批示后,方可凭此执行。
原料质量管理
第六条 原材料在采购进厂入库前,必须通知工艺技术科配合品质部进行常规检查。本着“随时进厂随时检验”的原则,不得延误。
第七条 技术、检验人员应依据质量检验标准进行检验。检验过程要严格按照有关质量标准和规定,采取合理的方法严格进行。
第八条 检验人员必须有高度的责任感和认真负责的工作态度,不得马虎、粗心,防止漏检和错检,更不能弄虚作假。
第九条 检验人员对每次的检验结果,应严格按检验单上表格所示内容进行如实填写,并签署本人姓名,作为责任依据。
第十条 只有经过检验达到质量标准,并由检验员签署“合格”的原材料,材料保管人员方能办理正式入库手续;否则,材料保管员将承担违规责任。
第十一条 检验时如遇到无法判定合格与否的情况,检验员应速向部门主管汇报或请求有关技术人员会同验收,判定合格与否。会同验收者也必须在检验记录单上签字。
第十二条 对于特殊重要物(如特别昂贵、特别稀有),应实行全检制度。
第十三条 对于随机抽样物,在发现有疑点时应反复多抽样,以防误差严重。
第十四条 需使用仪器等检测工具时,应经过校正,确认工具合格后方能使用。
第十五条 在进料检验时,若判定原料不合格,则填制质量异常处理表,报主管审批核准后,做出处理,必要时还须通知采购部门联络客户进行处理。
第十六条 检验人员依据情况,在必要时对所检材料向相关部门提出改善意见和建议。
第十七条 回馈进料检验情况,及时将原料供应商交货质量情况及检验处理情况登记于供应商资料卡内,供采购部门掌握情况。
制造前质量条件复查
第十八条 制造通知单的审核。
品质部主管收到制造通知单后,应于一日内完成审核。
1. 制造通知单的审核。
(1)订制品的特殊要求是否符合企业制造标准。
(2)种类。
(3)各项质量要求是否明确,是否符合本公司的质量规范;如有特殊质量要求是否可接受,是否需要先确认质量然后再确定产量。
(4)包装方式是否符合本企业的包装规定,客户要求的特殊包装方式可否接受。
(5)是否使用特殊的原材料。
2. 制造通知单审核后的处理。
(1)新开发产品试制通知单及特殊物理、化学性质或尺寸外观要求的通知单,应转交研发部提示有关制造条件等并签认。若确认其质量要求超出生产能力时应述明原因,将制造通知单送回制造部办理退单,由营业部向客户进行说明。
(2)新开发产品若质量标准尚未制定,应将制造通知单交研发部拟订加工条件及暂定质量标准,由研发部记录于制造规范上作为生产部门生产及质量管理的依据。
第十九条 生产前制造及质量标准复核。
1. 生产部门接到研发部送来的制造规范后,须由科长或组长先查核确认的事项。
(1)该产品是否订有成品质量标准及检验规范作为质量标准判定的依据。
(2)是否订有标准操作规范及加工方法。
2. 生产部门确认无误后在制造规范上签认,作为生产的依据。
制程质量管理
第二十条 生产部门在产品生产过程中要严格监控质量,做到四不:不合格的材料不投产,不合格的制品不转序,不合格的零部件不组装,不合格的成品不入库。要及时发现异常,迅速处理,防止扩大损失。
第二十一条 为保障过程质量,生产车间和技术部门应加强工艺管理,要不断地提高工艺质量,强化工艺纪律;要做好工艺文件的控制、工艺更改的控制、特殊工序的控制、不合格品的控制以及工艺状态的验证工作,使生产过程处于稳定的控制状态,从根本上预防和减少不合格品。
第二十二条 生产过程中的质量把关实行三检制:自检、互检、总检。
1. 自检。由各工段班组内部按照质量标准对自己的生产加工对象在生产过程中进行控制把关。
2. 互检。车间内部各工段班组之间,在下道工序接到上道工序的制品时,应检查上一工段的质量是否合格后方能继续作业。
3. 总检。由工艺技术科进行总体把关。
第二十三条 生产过程中申报检验的规定。
1. 操作人员在本工段生产完成后,必须经过质量检验人员实施首检确认合格后,方能转入下一工段继续生产。
2. 在自检与互检中,发现异常又无法确认是否合格时应及时报检。
3. 每个工段生产完成后转入下一工段时应报检。
4. 已形成产成品需入仓库时应报检。
第二十四条 异常情况发生的处理规定。
1. 生产部门在生产过程中若发现异常现象,应及时将信息反馈给当班生产主管进行处理;如因工艺备品质量或设备因素不能调整时,应向主管领导汇报,并立即停止生产作业,待找出异常原因并加以处理确认正常后,方可继续生产作业。
2. 技术、质检人员在抽检中发现异常时,应及时将存在的问题反馈至当班主管;如因工艺备品或设备异常问题得不到处理时,其有权责令停止生产作业,并向生产主管或相关领导汇报情况,待问题解决后方可继续进行生产。
3. 发现的异常原因与相关部门有关时(如原料问题属采购部门,设备故障原因属设备工段,工艺问题属工艺技术科),生产部门应及时通知或邀请各相关部门予以解决,不得延误。
4. 若有重大质量事故发生,应及时上报给上级主管直至生产部经理予以处理。
第二十五条 生产过程中关于不合格品的赔偿规定。
1. 生产过程中非人为因素造成的不合格品,不得追究操作者责任。
2. 属人为责任但操作者在自检中发现的不合格品,超出规定指标范围的操作者应承担所造成经济损失30%~50%的赔偿。
3. 在互检中发现的上一工段产生的不合格品,应对上一工段操作人员进行加倍的赔偿处罚。
4. 自检与互检均发生漏检和误检,被总检查出的,应对自检、互检人员同时进行赔偿处罚(见质量事故管理规定)。
5. 产品出厂因质量不合格被用户退货时,应对上述三方人员(自检、互检、总检)同时进行赔偿处罚。
产成品缴库管理
第二十六条 质量控制主管对预定缴库的批号,应逐项依制造流程卡及有关资料审核确认后,进行缴库工作。
第二十七条 质量控制专员应对缴库前的产成品进行抽检。若有质量不合格的批号且超过管理范围时,应填制异常处理单,详述异常情况并附拟订处理方式,报经理批示后,交有关部门处理及改善。
第二十八条 质量控制专员对复检不合格的批号,如经理无法裁决,应将异常处理单报总经理批示。
产品质量服务管理
第二十九条 质量服务管理应遵循的原则。
1. 上道工序责任部门和工段班组为下道工序服务。
2. 各相关部门要全力为品质部提供服务;同时品质部要及时将质量信息反馈到各部门,做好相互间的配合与协调。
3. 在不断提高工作效率的同时,须以保证质量为前提。
4. 销售为客户服务,生产为销售服务。
第三十条 销售部门应建立客户服务制度,制定客户服务计划,定期进行客户巡访服务活动。
第三十一条 对客户的巡访服务,主要包括以下五个方面的内容。
1. 向客户征询对产品的批评、建议、希望、申述,并进行调查分析。
2. 帮助客户解决使用产品过程中出现的技术、质量问题。
3. 及时向客户介绍并提供新产品和质量的改进信息。
4. 通过对客户的了解,深入调查研究产品在各个市场区域的销售状况,掌握市场对产品质量标准的要求与变化。
5. 及时做好产品质量信息的收集与反馈工作,合理地提出产品质量改进的建议与意见。
第三十二条 对客户投诉事件的处理。
1. 销售部门在接到客户投诉反映的产品质量问题时,应立即查明相关资料(订单编号、产品规格型号、数量和金额、发货日期、客户要求、产品工艺技术方案和质量标准)并填制客户投诉处理表,报送主管签批处理意见。
2. 销售部门将签批的客户投诉处理表传递并会同相关部门(工艺技术科、品质部、生产车间)进行质量事故调查分析与责任认定,提出解决处理的方案,编制质量事故分析报告,报主管经理审核决策。
3. 销售部门将拟订的质量事故处理的方式与结果,向客户说明缘由并进行交涉;待到双方都对结果满意时,向主管报明情况,执行处理结果。
4. 对质量责任者的处罚,分部门或个人按质量事故管理规定执行。
5. 认为客户投诉不成立时,由销售部门负责做好与客户的交涉工作。
第三十三条 产品质量意见的征询与处理。
1. 每批产品在发货出厂前,应由销售部门会同品质部门编制产品质量意见征询表,并随同产品合格证一并发至客户手中。
2. 销售部门在巡访时,将客户对产品使用意见情况、质量要求和改进建议填至产品质量意见征询表相关栏目中,并请客户签字确认。
3. 销售部门调查分析市场上同类产品、替代品、新产品的质量情况,并做出对比分析,查找产品质量的优点和不足,提出质量改进的意见。
4. 销售部门定期收集、整理、分析产品质量意见征询表,及时反馈给主管领导和相关部门;必要时还应组织召开质量分析专题会议,针对客户所提意见进行讨论分析,制定改进措施,完善质量标准,提高产品质量。
质量事故处理
第三十四条 因客观原因(如雨季、沙尘暴)造成的质量问题,应由品质部与工艺技术部主管亲临现场协商处理,并将结果上报主管领导审核。
第三十五条 对于生产过程中因操作不当或责任心不强、检验人员工作疏忽等主观原因造成的质量问题,应由销售部派人走访客户,对用户提出的问题进行现场验证,依据给其造成的损失及影响大小提出解决处理办法。
第三十六条 对于因主观原因造成的质量事故,事业部要认真进行调查分析,进行产品质量追溯,认定质量责任,进行严肃处理。
第三十七条 责任质量事故的分类。
1. 一般事故(经济损失在1万元以下)。
2. 重大质量事故(经济损失在1万~10万元)。
3. 特大质量事故(经济损失在10万元以上)。
第三十八条 对各类质量事故的处理。
1. 一般质量事故。未造成经济损失的,销售部派出调查人员的费用由责任部门或个人承担;造成经济损失的,由责任部门或个人承担70%~100%的损失。
2. 重大质量事故。根据造成的经济损失和情节严重程度,由责任部门或个人承担50%~80%的损失。
3. 特大质量事故。造成的经济损失由责任部门或个人承担30%~100%的损失,并对主要责任领导给予行政处分。
4. 发生重大、特大质量事故的,车间主管是主要责任人,对责任领导分别处以2000~5000元的罚款,并加以行政降职或撤职处分。
第三十九条 属于检验人员工作失误造成的质量事故,应根据事故性质和损失大小,给予责任人罚款、停职、辞退等处理,并相应地追究主管领导的责任。
第四十条 因各部门管理不严造成的质量事故,应根据事故性质和损失大小,对主管领导进行罚款、降级、撤职等处理。
第四十一条 各工段班组在自检过程中,对于发现质量问题隐瞒不报,致使事故扩大并造成一定经济损失的,应根据损失大小对直接责任人加倍进行处罚。
附则
第四十二条 本制度报总经理核准后实施,修改时亦同。